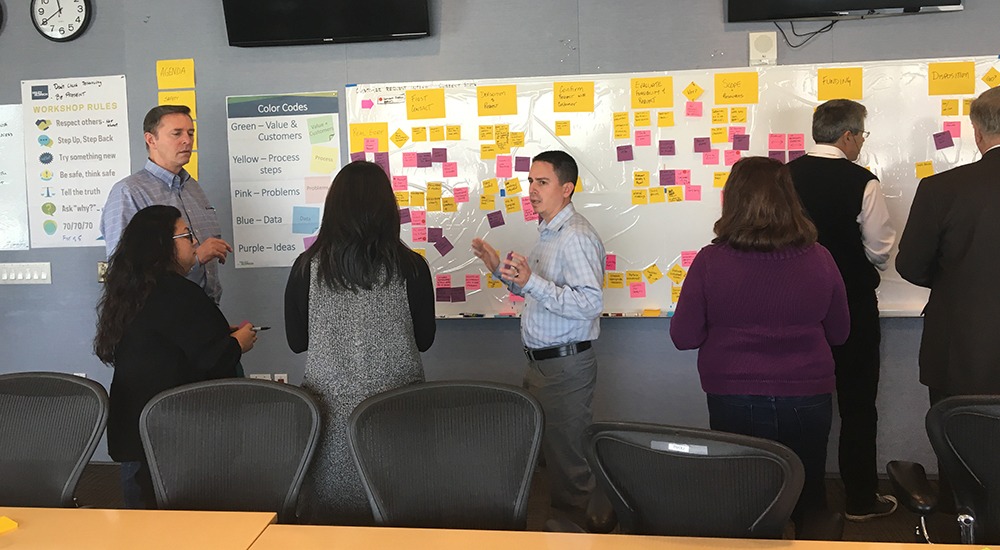
Higher education
A California university integrates Lean principles to streamline roles and collaboration
7 departments
across which we shifted culture
80%
of capital projects for which we stabilized delivery processes
90%
of high-impact ideas implemented
Summary
- Leaders at a large California university aimed to grow their health science initiative. Their decade-long plan would involve cross-department capital programs, real estate planning, and other major projects. But they had to overcome a siloed organizational culture.
- They turned to our Lean experts for help adopting a management approach that would motivate break down silos and motivate employees to solve problems together.
- We engaged more than than 200 individuals across campus in a multiyear effort to streamline projects, departments, and systems.
- Our team realized results by integrating teams involved the supply chain process, streamlining roles and duties, and a building trust and a common vernacular across the health science project team.
Client challenge
Leaders at a large West Coast university sought to advance healthcare worldwide through its healthcare and research-focused institution. To deliver on this vision, they expected the effort would take at least 10 years and significant investment across departments to complete — including capital programs, real estate, planning, supply chain, and other critical stakeholders. The university’s rapid growth and increasing demands exposed an issue prevalent in many higher education institutions; that is, inefficiencies and challenges caused by siloed departments. As a result, staff were stressed and felt overburdened rather than empowered and engaged.
University leaders knew they needed a management approach that would work well with their grassroots, collaborative culture and motivate their employees. Not only that, they were seeking a solution they could continually turn to that would help them remove future obstacles, and efficiently and effectively address problems as they emerged.
Lean is a principle-based way of thinking and acting that has three main tenets: increasing value, respecting people, and reducing waste. Lean was a natural fit for the university, as was partnering with Haley & Aldrich to implement the methodology. The university decided to work with Haley & Aldrich largely because we share similar collaborative cultures and empower people to bring about transformational change.
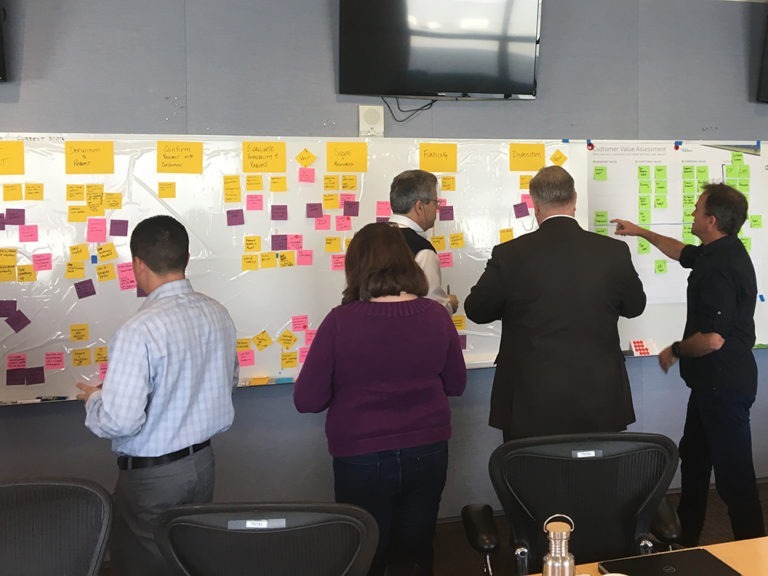
Our approach
Starting in 2013, Haley & Aldrich’s practitioners and facilitators partnered with seven departments and more than 200 individuals across the institution’s campus to address complex challenges using a Lean approach. This included single projects, department-wide and interdepartmental processes and systems, training, and strategic university efforts.
Throughout our work, we relied on Lean principles and Haley & Aldrich’s standard strategy development and process improvement approach. We utilized the value of our Lean practitioners: the ability to tap into and uncover the full potential of each team member. We showed respect for individuals — whether a front-line electrician or a department head. This empowered every team member to contribute their creativity, knowledge, and intellect to create more effective overall processes and develop sustainable changes in behavior.
We have applied this approach in numerous instances over the course of our work with the university, including the following:
Building a Lean culture by improving capital projects processes
Haley & Aldrich worked with the capital programs team to improve their processes by lowering the cost and accelerating project delivery. Our Lean facilitators led a series of workshops and worked with the team to reorganize project delivery processes, assess the organizational structure, and make recommendations regarding skill sets, roles, and responsibilities of the team’s leadership. Soon, adjacent departments were exposed to Lean principles in their work with the capital programs team and experienced the tremendous value and efficiency of Lean thinking. As a result, Haley & Aldrich practitioners taught Lean Fundamentals classes to other staff and departments, not only introducing them to Lean principles and tools, but laying the groundwork to build a cross-departmental Lean culture for continuous improvement.
Creating an integrated supply chain organization to support departments across the university
University leadership recognized that procurement processes needed to be integrated across the campus. Different departments handled procurement themselves, resulting in duplicate efforts, redundant roles, and higher costs. We brought together stakeholders in capital programs, facilities, supply chain management, and finance, as well as strategic suppliers, to create the first integrated supply chain organization of its type.
The goal of the integration was to enable huge growth at minimum total cost for the university through gaining economies of scale, improving processes, and maximizing the contributions of all individuals so their work was uniquely valued and integrated effectively. Our improvement approach included clearly defining roles and responsibilities based on the functional needs of the university, as well as agreeing to reasonable timelines, creating transparency in systems and processes, and building a sense of shared accountability for achieving goals.
Building a high-functioning team for a new health science research facility project
Through Haley & Aldrich-facilitated Lean workshops, we helped to create a high-functioning team and improve project performance on a multimillion-dollar health science research real estate project. To do so, we engaged more than 40 team members — including trades partners, foremen, superintendents, architects, and project managers. The result? All team members felt a shared sense of accountability, which encouraged more direct and clear communication and empowered team members to speak up when confronted with an issue.
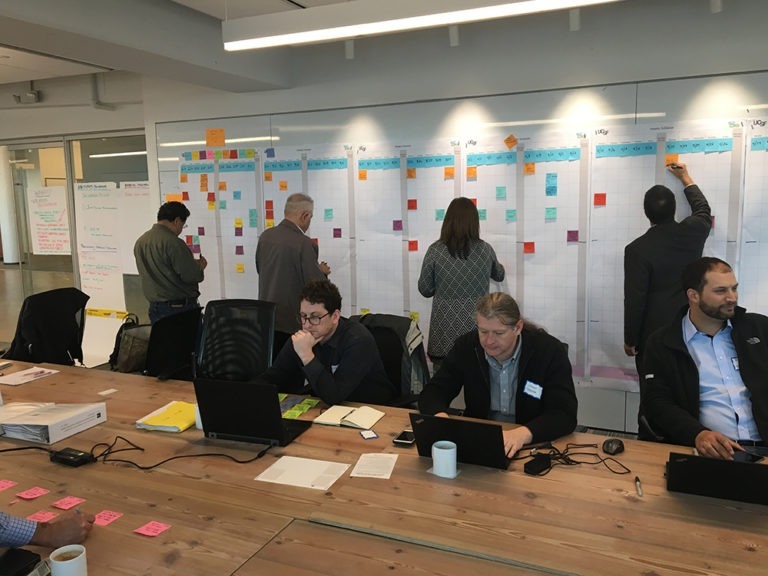
Value delivered
- Fostered a culture shift across seven departments from one with hidden problems and a lack of transparency to one of openness, respect, and collaboration
- Stabilized 80% of capital programs project delivery processes and reduced the team’s time to perform the work
- Integrated more than five teams involved in the supply chain process, streamlined roles and duties, built trust and a common vernacular among teams, and simplified the supply chain process so that work could be completed more effectively and efficiently
- Created a culture of collaboration and respect among all health science project team members that resulted in implementation of 90% of the high-impact ideas the project team identified, ultimately saving time and reducing waste
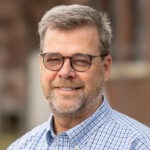
Program Manager, Geology