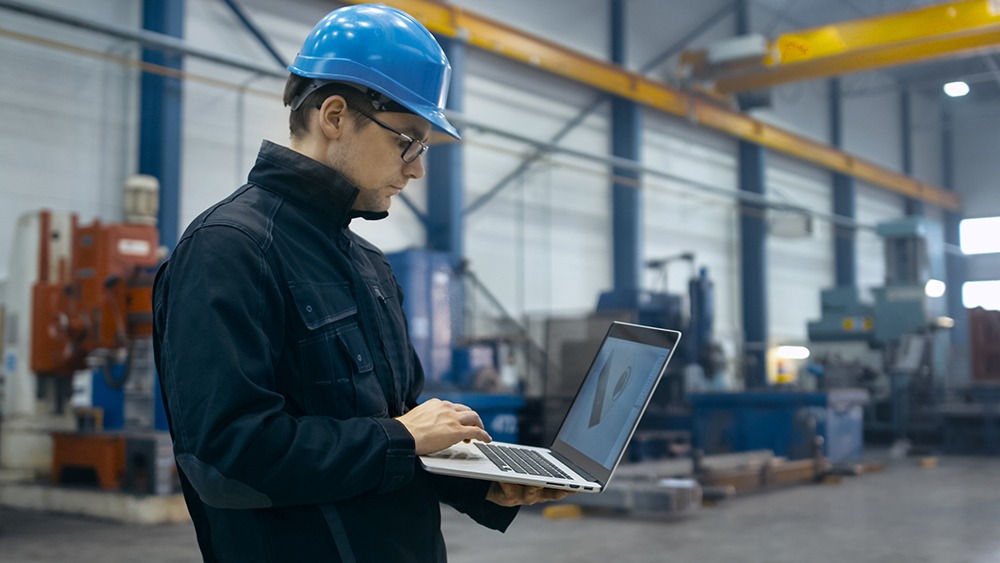
Automotive
Engine manufacturer saves time, money via regional compliance audit innovation
$50,000
projected amount saved by our self-audit tool
Summary
- A global manufacturer needed to make sure newly acquired facilities upheld its strong brand reputation.
- Our team conducted environmental health and safety audits on the facilities in just eight weeks to confirm their compliance with corporate standards and regulations, giving the client enough time to expedite any necessary changes.
- To help the client make strategic business decisions on a regional or site-specific basis, we created an adaptive auditing tool that provided at-a-glance results and delivered actionable, prioritized information.
A global manufacturer of engines and power generation products took ownership of previously franchised nationwide distribution and repair facilities and wanted to quickly ensure these new assets upheld the manufacturer’s strong brand reputation with customers.
The manufacturer sought a partner who could conduct environmental health and safety audits on the facilities in just six to eight weeks to confirm their compliance with both corporate standards and applicable regulations. Key to meeting this time frame was creating an audit reporting format that could provide the necessary information in the time allocated to meet the deadline.
After working with the client on a few initial audits, Haley & Aldrich came up with an adaptive approach that resulted in a concise, at-a-glance report that allowed the client to make quick and efficient strategic business decisions.
Our approach
Haley & Aldrich knew the client’s ultimate goal was to expedite any necessary changes to ensure these distribution centers, now part of the manufacturer’s business operations, upheld the brand’s reputation. But to make those business decisions, the manufacturer needed good data — and fast. The traditional approach for presenting auditing data was lengthy, text-heavy Microsoft Word documents. This meant the client would be tasked with the cumbersome process of manipulating and analyzing individual site data, requiring the client to take additional steps to uncover usable regional information.
This was at odds with the client’s need for a regional snapshot of identified compliance issues across its diverse service facilities portfolio that would allow for strategizing on completing similar tasks across the locations and enable consistent application of corrective actions. To meet that need, we created a Microsoft Excel-based auditing tool that spans the audit process, from pre-audit communications to in-field documentation and final reporting. The tool not only improved the auditing efficiency necessary to meet the client’s tight schedule, but also delivered data in a format that included a regional summary dashboard linked to individual site reports on subsequent workbook tabs.
This audit tool gave the client a holistic view of the regions, and because we designed it to summarize changing data in a consistent and repeatable fashion, can now be used to self-audit, resulting in considerable future time and cost savings.
Value delivered
- Developed an adaptive Excel-based auditing tool that consolidates data into a heat map to provide at-a-glance accessibility
- Delivered actionable, prioritized information that the client can use to make strategic business decisions on a regional or site-specific basis
- Helped the client realize approximately $50,000 in future time and cost savings by using the tool to self-audit
For more information, contact:
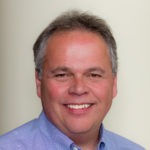
President and Chief Executive Officer
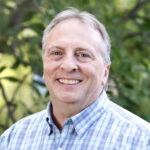
Senior Project Manager