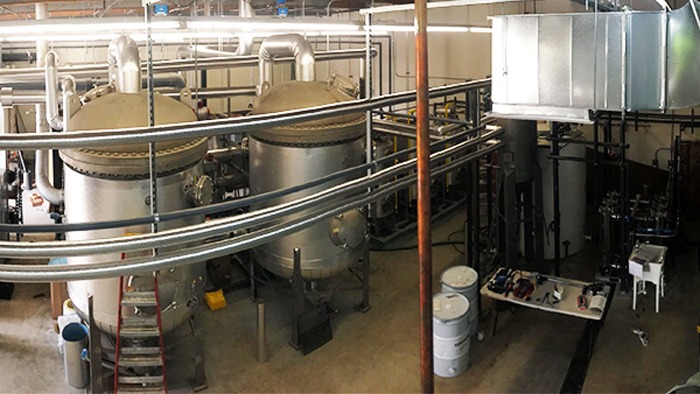
Aerospace
Client saves $2.5 million, meets regulatory deadline through innovative treatment design and holistic project management
$2.5 million
saved in capital costs
24/7
operations maintained for all tenants
Summary
- Haley & Aldrich helped a client remediate trichloroethylene contamination at active multi-tenant properties.
- Our approach accounted for risk management, balanced stakeholders’ objectives, and incorporated an innovative technical design.
- We saved the client $2.5 million in original-design capital costs by designing and constructing a system in an existing suite, rather than building a new compound for it, and optimizing the design and operations of the system.
- We also completed the work on time and within budget safely and without obstructing tenant’s 24/7 operations.
Client challenge
Through an acquisition, a confidential client became the responsible party to remediate trichloroethylene (TCE) contamination on active, multi-tenant properties. The client needed to remediate the soil and groundwater, but first had to secure access rights from the property owners. Because of the tight quarters and busy 24/7 tenant operations, the client needed an unobtrusive remediation system that would not impede the active tenants’ operations and fit into a small suite in a 10-suite building. So the client called on Haley & Aldrich for our teams’ considerable experience and reputation in chlorinated solvent remediation, our ability to work with stakeholders like tenants, owners, and regulators to meet the needs of all, and our innovative approaches that address complex situations like this.
Our approach
We recognized the challenge as not just a technical one, but one requiring overall risk management and the balancing of all stakeholders’ objectives. We initiated our work with kickoff meetings with our client to lay out the management, financial, health and safety, design, construction, and operational risks and challenges. We identified a solution for each risk. We then met weekly with our client throughout the project to make adjustments and identify emerging risks. We engaged with the regulators, owners, and tenants as partners to help resolve access and remedy implementation challenges. This helped secure a practical and expedited schedule as well as a cost-effective implementation.
Our innovative design is a soil-vapor and dual-phase extraction system that uses regenerative resin for treatment of the vapor and water streams. Other treatment methods require a larger footprint than the suite space allows; large trucks to service the system frequently, which is disruptive to the owners and tenants; and treatment effluent levels not favored by our client and regulators. We use automated multiple resin beds to remove contaminants and steam to regenerate the resin, minimizing waste streams and resources while ensuring continuous operation of the system.
Value delivered
- Saved the client $2.5 million in original-design capital costs by designing and constructing a system that can be housed in an existing suite, rather than building a new compound for it, and in optimizing the design and operations of the system
- Completed the work on time and within budget safely and without obstructing tenant’s 24/7 operations
- Navigated the many permit and utility requirements and streamlined approvals and buy-ins by engaging all stakeholders in the solution
For more information, contact:
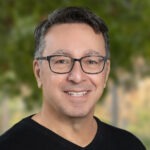
Principal Consultant