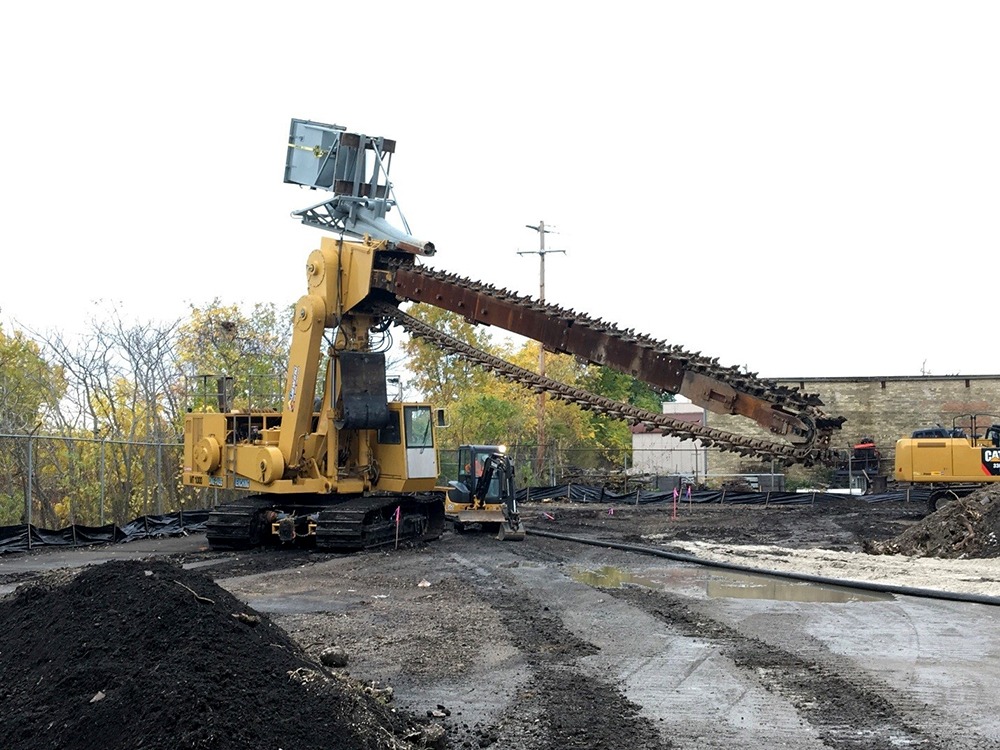
Manufacturing
Design/build team remediates brownfield site under budget and on time
$45,000
saved on permitting costs
Summary
- A manufacturing client relied on our help to clean up a brownfield site and successfully navigate a compressed construction schedule, without increasing costs.
- With a detailed project plan, we met all the client’s objectives, incorporating teamwork, efficiency, and schedule management to design and construct a cap and containment solution.
- We also refined the budget and reduced labor costs by maximizing equipment operator use and sequencing and consolidating tasks accordingly, completing the project under budget and on time.
Client challenge
After decades of industrial use, a contaminated site owned by our manufacturing client was deemed a brownfield. Previously used as a wastewater treatment and hazardous material storage area, the resulting contamination posed a threat to groundwater. When approached to remediate the site, Haley & Aldrich was also faced with the challenge of an extremely compressed construction schedule that required us to meet key regulatory milestones and a fast-approaching winter. With only five days of float in the schedule, any delays would push the project into the spring adding significant time and remobilization costs. The site’s location in an urban environment also posed inherent security risks. Our reputation for overcoming challenges and maintaining tight schedules was critical for keeping this repeat client.
Our approach
The Haley & Aldrich design/build team used a detail-oriented project planning approach to meet the client’s objectives. Understanding that a high level of teamwork, efficiency, and schedule management was crucial to achieving critical path milestones, we committed our design and construction resources to design and construct a cap and containment solution that included a slurry wall, perimeter toe drain, and asphalt cap. Unexpected lead contamination in the soil was encountered during construction which required the stabilization of the additional impacted soil.
Through a design/build approach, we refined the budget and reduced labor costs by maximizing equipment operator utilization and sequencing and consolidating tasks accordingly. We approached problems as a unified team setting the expectation that each functional group would meet the schedule and budget for our client. We completed the project under budget and prior to temperatures dropping to the point where the local asphalt plants shut down.
Value delivered
- Integrated multiple design/build services to facilitate a shortened schedule
- Delivered a challenging design/build project cost effectively and on time
- Mitigated unforeseen site conditions with minimal impact to the project budget
- Saved a net $45,000 on permitting costs by using an available code variance
For more information, contact:
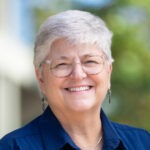
Principal Consultant