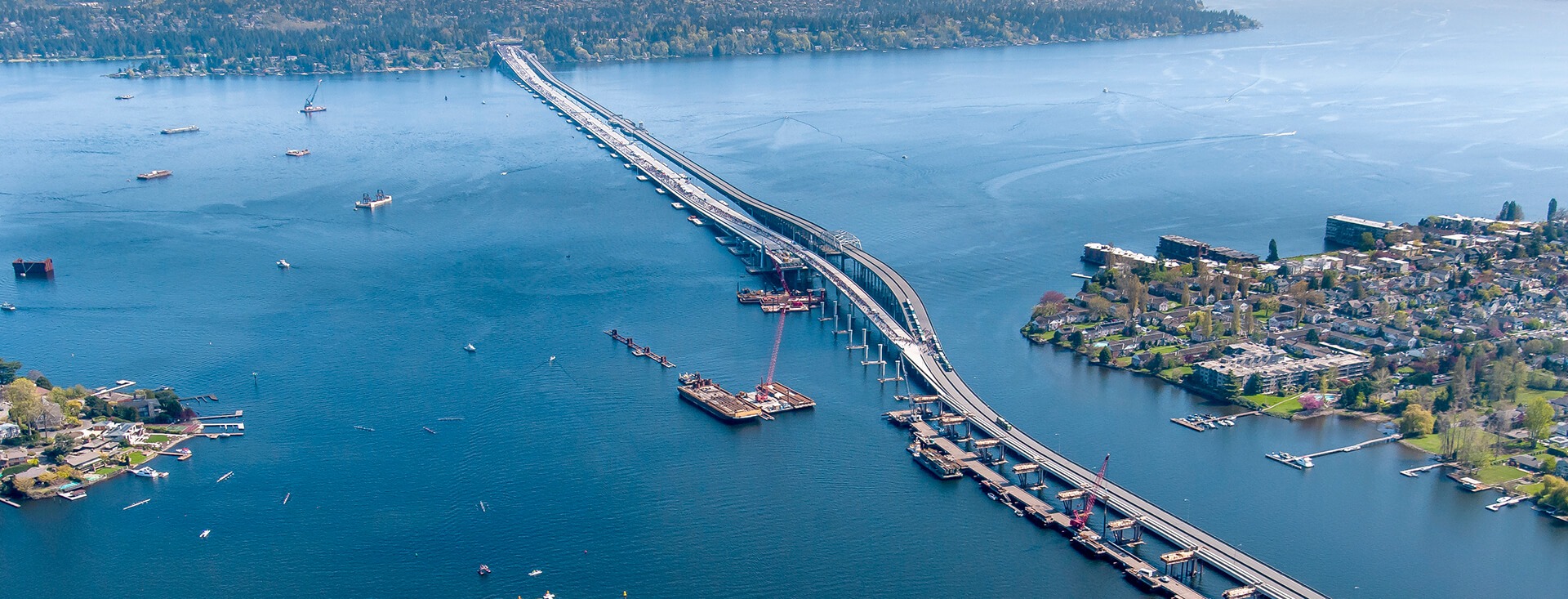
Transportation
Geotechnical ingenuity and site-specific anchor design overcome challenges to build world’s longest floating bridge
7,710 feet long
floating span, certified the longest in the world when the bridge opened
89 miles per hour
sustained wind speed it is designed to resist, 32 mph faster than original bridge
74,000 motorists
cross bridge each day, on average
Summary
- The Washington State Department of Transportation (WSDOT) needed a replacement for the Evergreen Point Floating Bridge, a stretch of State Route 520 that spans Lake Washington to connect Seattle with communities to the east.
- The new bridge needed to handle more traffic, accommodate mass transit, and hold up under high winds, waves, seismic seiches, and other environmental forces.
- But meeting these goals would be challenging, given the difficulty of testing the very soft site soil under the lake, the extreme weather possible in the Pacific Northwest, and the need to withstand seismic activity.
- The WSDOT and the design/build contractor, Kiewit, trusted Haley & Aldrich to design anchors for a new floating bridge, given our familiarity with the area’s risk factors and our proven track record of designing for resilience.
- Collaborating closely with other project partners, we took a site-specific approach to anchor design. We used three different types of anchor tailored to specific conditions along the bridge’s path, an approach that enabled us to match anchor design and materials to the exact soil conditions, water depth, environmental constraints, and navigation requirements of each site.
- This tailored solution helped deliver a bridge with an expected 75-year life span while also saving the WSDOT money and minimizing environmental impact to the lake during construction.
Client challenge
The WSDOT needed a replacement for the Evergreen Point Floating Bridge, a section of State Route 520 that connects Seattle with communities to the east. The new bridge needed to handle more traffic, accommodate mass transit, and better withstand high winds, waves, seismic activity, and other environmental forces.
The original bridge, a critical corridor for commuters across Lake Washington, had deteriorated after more than 50 years of use. Its support columns were vulnerable to windstorms, waves, and earthquakes, and its weakened pontoons needed to be replaced. It regularly closed to traffic during sustained high winds, meaning a constant threat of disruption for commuters.
A floating bridge design still made the right replacement for the old structure. Soil suitable for bearing the weight of the bridge was deep below the lake’s surface — at depths exceeding 300 feet in some places — which would make a more conventional structure, like a suspension bridge, prohibitively difficult and costly to construct.
But a large, environmentally resilient floating bridge would still pose many design and construction challenges. The new bridge’s anchor design would need to have the capacity required to withstand the region’s strong storms and seismic seiche waves induced by earthquakes. The anchors would have to be extremely deep to reach the dense soils below the mushy silt and sediment. And with 200-feet-deep water and the additional 100 feet of soft, highly compressible soil beneath that, the project team faced difficulty collecting soil samples and understanding conditions beneath the surface.
The WSDOT relied on our geotechnical engineering team to design an anchor system that would hold up under extreme conditions and deliver the minimum 75-year life span desired for the new bridge. We brought an extensive understanding of the region’s seismic risk factors as well as a proven track record of designing for resilience.
Our approach
Our team knew that this technically challenging project would require geotechnical ingenuity and fluid collaboration with the rest of the project team. Together, we had to meet extremely large anchor capacity requirements and work with subsurface conditions that we couldn’t analyze in detail, but that we suspected to be highly variable.
After determining that new subsurface testing would cost our client dearly but would not likely reveal useful data, we relied on existing data from testing that had been conducted on anchors for an adjacent floating bridge, which allowed us to reasonably approximate the soil strength measurements needed to design specialized anchors for the new Evergreen Point Floating Bridge.
We took a site-specific approach to designing the anchors, ultimately using three different types (drilled shaft, gravity, and fluke) tailored to conditions along the bridge’s path. This approach enabled us to match anchor design and materials (reinforced concrete, steel, and ballast rock) to the exact soil conditions, water depth, environmental constraints, and navigation requirements of each anchor site, ultimately increasing reliability.
Our team designed the anchors to withstand lateral loads five times higher than previous floating bridge anchors in the state. These designs also allowed our client to add more ballast rock in the unlikely event that the anchors begin to slip — a comparatively inexpensive and easy fix. To ensure that the anchors located in deeper waters could still withstand significant winds, waves, and seismic seiches (earthquake-generated waves that can last for hours or even days), we modeled for and placed targeted ballast rock in front of the anchors, which proportionately increases their pull-out resistance. The final anchor design resulted in a 62 percent increase in anchor surface area, while the anchor capacity increased by nearly 500 percent.
This approach also resulted in significant cost savings because we relied on relatively common, conventional construction materials. We revised WSDOT’s initial anchor design to allow for a greater lateral capacity, and we used a gravel pad and precast teeth on the gravity anchors to increase frictional resistance by nearly 67 percent, which saved money by reducing the sizes of the anchors and the amount of ballast fill and dredging required to complete the project.
How we minimized environmental impact
- Through design features, reduced dredging needs and construction footprint, which lessened the impact on the lake’s ecosystem.
- During excavation, used steel containment casings and work platforms to reduce sediment released into the air and water.
- Minimized installation noise and vibration effects on fish by lowering anchors to the lake floor and using pressurized water (i.e., jetting) to push them into the soft soil.
- Chose construction materials that wouldn’t leach contaminants.
Finally, we didn’t leave anchor performance to chance. Through comprehensive load testing on each anchor, we ensured the reliability of the bridge before, during, and after a major storm or earthquake. This testing increased the WSDOT’s confidence in the anchors’ performance.
The new bridge, which opened in 2016, stretches 130 feet longer than the bridge it replaced. It rests on 77 support pontoons — more than twice as many as the previous bridge — many of which are longer than a football field and three stories high. The new bridge also has six lanes, four more than its predecessor, with one dedicated bus and carpool lane running in each direction. The design can also accommodate an expansion of the state’s light rail system across the bridge.
Value delivered
- Provided the public with a safer, greener commuting option in a crucial traffic corridor
- Delivered on a new bridge with a 75-year life span and with increased capacity to handle traffic, adapt for public transportation use, and withstand seismic and other environmental stressors
- Took a site-specific design approach that made use of three anchor types and conventional materials to reduce costs and increase stability for the new bridge
- Minimized environmental impacts during construction
For more information, contact:
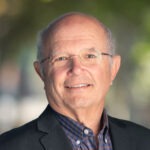
Senior Principal Geotechnical Engineer