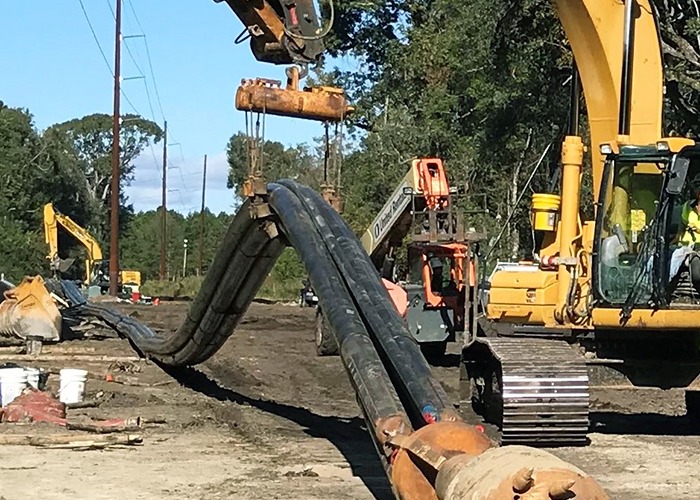
Electric transmission and distribution
We helped preserve wetlands and client reputation while installing cables with horizontal drilling tech
Summary
- Central Electric Power Cooperative (CEP) needed to add redundancy to its infrastructure near the South Carolina coast to guard against power outages.
- To accomplish this, CEP had to install power cables underneath protected wetlands and historic trees. If the project disturbed the trees, CEP would incur hundreds of thousands of dollars in fines.
- We brought experience managing horizontal directional drilling in similarly difficult conditions. After carefully assessing the site, we found a cost-effective, risk-reducing solution to drilling and installing wires in its loose sands.
- We also protected CEP’s reputation with the public and regulators through proactive communication and management of stakeholder expectations.
Client challenge
CEP needed to insure South Carolina distribution cooperatives and residents against power outages by adding redundancy to their infrastructure near the coast. Fulfilling that vision required the power generation and transmission nonprofit to connect a substation on a small island to a power line on another. Connecting the infrastructure required installing 115-kilovolt power cables underneath more than a half-mile of protected estuaries and salt marshes. At the same time, CEP had to preserve trees that, if disturbed, would incur hundreds of thousands of dollars in fines.
CEP needed an engineering team it could trust to design a horizontal directional drill (HDD) crossing that protected Bohicket Creek and its reputation. The company counted on Haley & Aldrich to safely weave the cables through the wetlands because of our experience anticipating and balancing risks while navigating similarly challenging conditions.
Our approach
Despite our deep understanding of the local geology, we knew protecting the wetlands and preventing inadvertent returns required us to be certain what lay beneath the subsurface. To best manage risk to the project, we took three times the normal number of borings required for HDD and quickly confirmed what we suspected: The crossing needed to be bored through loose sands that would collapse the minute we drilled through them. The typical solution — encasing the smaller, more flexible pipes within a larger, more rigid pipe — would have required spacers and thermal grout, increased the diameter of the borehole, and escalated project costs. So, we recommended and designed conduits that could be pulled into the borehole as a bundle without using casing pipe. This method reduced our client’s risks, liabilities, and saved it money.
Drilling in the wetland environment was particularly tricky. To prevent any major damage, we carefully chose the HDD’s entry and exit points and monitored the construction itself to watch for inadvertent returns. During the project’s critical stages, such as pipe pullback, our staff worked extra hours to ensure the project team did not violate permit requirements and that they fused and handled conduits according to the specifications. We also monitored the alignment for drill fluid releases and implemented the inadvertent return contingency plan. Working closely with the drilling contractor, we addressed problems as they occurred and quickly negotiated solutions between the contractor and with the U.S. Army Corps of Engineers.
During drilling, the friction and loads got so high that the pipe might have been compromised, so we suggested that our client have a specialist inspect the pipe. The specialist repaired and reused the compromised pipe section and signed off on its integrity. Through our oversight, CEP was able to avoid this potential cost overrun. As a result, we kept the project within budget and on schedule to meet CEP’s in-service date.
Value delivered
- Enhanced CEP’s reputation with the public and regulators by proactively communicating with CEP’s project manager, eliminating surprises, and allowing him to control the project’s costs and schedule while meeting stakeholder expectations
- Preserved live oak trees predating the Civil War and spared our client massive fines by designing the pipe conduit with 167 joints, giving it the flexibility to bypass the trees
For more information, contact:
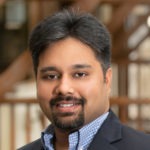
Senior Technical Expert, Civil Engineer and Trenchless Practice Leader