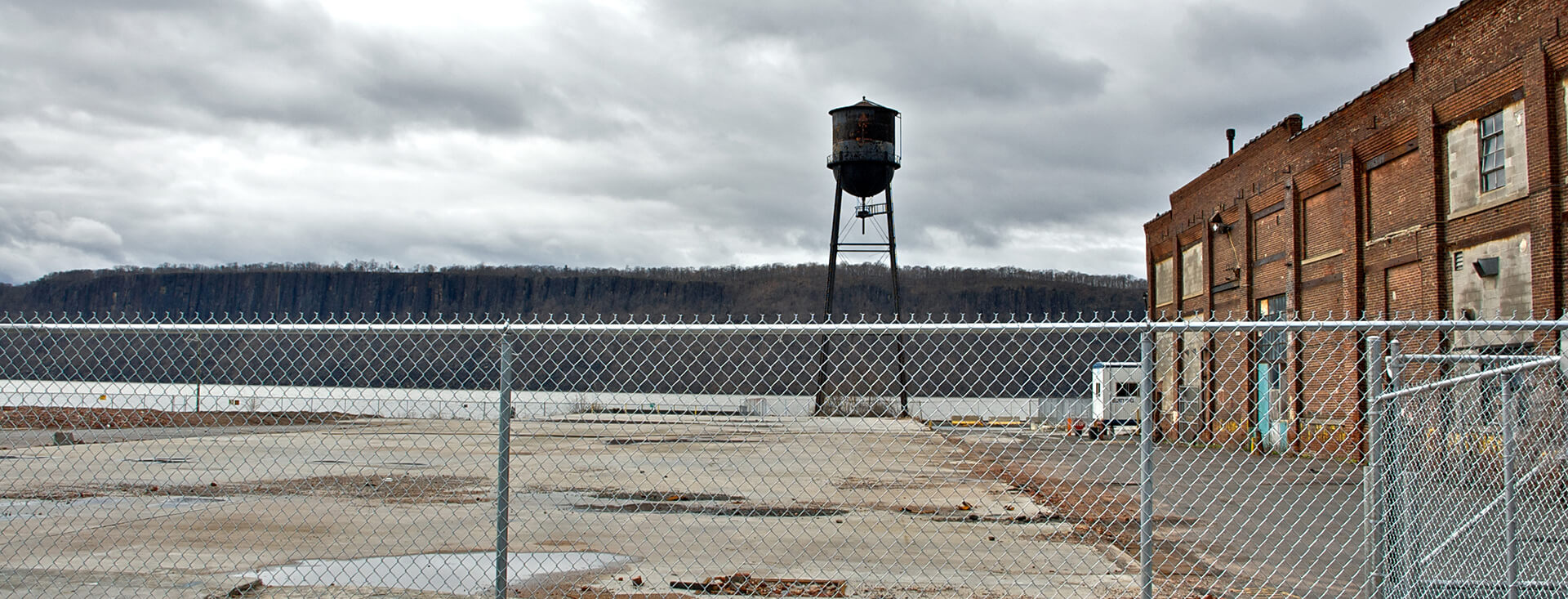
Manufacturing
Oil and gas company saves millions and maintains good community relations
$200,000
saved with process efficiencies
$200 million
saved by client
Summary
- A multinational oil and gas company discovered that it had purchased an industrial site contaminated with PCBs and retained Haley & Aldrich to help with the remediation plan.
- We shaved $200 million off the original plan by collaborating with regulators and the community to incorporate alternate engineering designs that met cleanup objectives.
- We also helped our client maintain a positive relationship with the community by buying local and strengthening relationships with local leaders and agencies.
- Using Lean thinking, we removed nearly $200,000 in waste from the process, dramatically improving workflow and work environment and delivering faster results for the client.
Client challenge
An oil and gas company purchased an industrial conglomerate only to discover one of the packaged properties would become one of its largest legacy liabilities. PCBs attributed to a World War II–era cable manufacturer were identified in the onshore soils and Hudson River sediments and needed to be cleaned up. During Haley & Aldrich’s review of the planned remedy, new data revealed not only that it was not constructible, but implementing the remedy would have required extraordinary measures. Moreover, our client would have incurred unexpected costs, and the site could have met further setbacks on the road to redevelopment. To realize its end vision, our client needed us to revise the approved remedy and convince the New York State Department of Environmental Conservation (NYSDEC) and an active local community to endorse it.
Our approach
Changing the approved remedy’s scope and direction required tapping into our strengths as geotechnical engineers, risk assessors, and hydrogeologists as well as communicators and negotiators. We proved the deep dredging and excavations outlined in the original remedy could not be supported by the proposed structures and slopes, particularly given the presence of contaminants below the water table.
Once we identified the precise location of the subsurface contamination, our fate and transport experts showed other aspects of the original remedy would have contaminated an otherwise clean aquifer. We put the community’s mind at ease by demonstrating that unique site conditions reduced risks to human and environmental health.
Ultimately, we persuaded NYSDEC to approve a targeted, whole-site approach that combined upland and sediment operable units into one remedy. Our new remedy dredged only the areas posing the greatest threats, significantly limited onshore excavation, and encapsulated the impacted sediments in areas where disturbing sediments and soils would have cost tens of millions more and could have made the situation worse.
Value delivered
- Saved our client $200 million by collaborating with regulators and the community to amend an existing Record of Decision to incorporate alternate engineering designs that would meet the remedial objectives.
- Helped our client maintain a positive image within the community by “buying local” and actively pursuing relationships with local leaders and agencies.
- Removed nearly $200,000 in process waste using Lean thinking, dramatically improving both workflow and work environment and delivering faster results for the client.
“This project was unique because we not only developed a new approach to address the met challenges, but our method was backed by the community.”
Keith Aragona, Haley & Aldrich
For more information, contact:
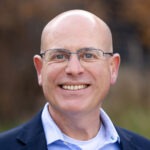
Senior Project Manager, Manufacturing