I recently had the privilege of listening in on a Haley & Aldrich-hosted industrial client peer group discussion. These manufacturers shared the various challenges their companies face as staff begin returning to work following stay-at-home orders. Despite coming from different industries and organizational structures, they are dealing with similar employee safety concerns.
As well as sharing the key challenges they raised, I’ll also share some of Haley & Aldrich’s resources and guidance to getting operations running again while keeping employees safe.
Testing employees at the facility
One company has put a system in place that could test employees at their large facilities, and another is exploring testing to enable them to expedite the return of staff who had already tested positive and been quarantined. Both companies would test only in response to an identified positive case. It’s important to note that the Equal Employment Opportunity Commission does not permit employers to conduct antibody testing, but does allow viral testing so employers can prevent infected people from entering workplaces.
Tracing contacts
Some of our manufacturing clients have started contact tracing following Centers for Disease Control and Prevention (CDC) guidelines and Health Insurance Portability and Accountability Act of 1996 (HIPAA) rules, which involves the identification, monitoring, and support of the individuals (contacts) who have been exposed to the patient and possibly infected themselves. Our participants said they are either already using–or considering the use of–the federal guidance.
Our guidance: If someone is identified as having COVID-19, we advise implementing a tracing program like CDC’s 6 feet/15 minutes/48 hours prior recommendation. This requires you to determine who among their coworkers have been within 6 feet of for 15 minutes or more of the employee within the last 48 hours, and then ask those coworkers to stay home for 14 days, monitor themselves for symptoms, and practice social distancing. Some of our clients have incorporated an electronic self-declaration that makes searching for contacts faster and easier should an employee become infected with COVID-19. Haley & Aldrich has done this too, as it allows us to identify employees who have been around each other at work, allowing us to trace potential contacts.
In cases that involve individuals outside your company, inform the external parties to help them perform contact tracing. To identify what’s working and what’s not internally, conduct drills of your contact tracing program to simulate your tracing process.
Experiencing regulatory confusion
According to the peer group manufacturers, regulators are inconsistently guiding manufacturers on how to navigate and comply with COVID-19 related requirements, so keeping up with the constantly changing requirements in various states and locations has been arduous.
Our guidance: With so many requirements and guidance resources, consider customizing health and safety plans to include links for each office’s state, county, and local COVID-19 regulations so that the information is always easily accessible and up to date. We’ve provided a COVID-19 State and Local Policy Dashboard to help you find the latest regulatory information on a state-by-state basis (with a toggle on the top right for the local county level).
Bridging the work-home divide
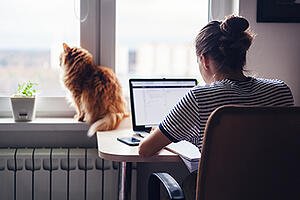
Companies are emphasizing personal health and safety practices both at work and at home including hand washing and social distancing in common areas. They recognize that employees’ home habits impact the risk of COVID-19 in their workplaces too.
Our manufacturing clients quickly accepted that many of their staff whose work does not require them to be on the manufacturing floor are teleworking now or might be in the future.
Our guidance: Consider distributing fact sheets and infographics on various topics such as ergonomics, how to wear a mask, and what to do if you think you are becoming sick to provide consistent guidance and practices for your employees. Haley & Aldrich has made these available on our intranet and promoted them in Health & Safety virtual meetings.
Making masks mandatory
Most participants in the peer group discussion said their companies have required social distancing and face coverings. For several manufacturers, employees have been reluctant to voluntarily use face masks. One client representative indicated they want their company to make face coverings mandatory, as even cloth masks are a worthy line of defense to mitigate the COVID-19 pandemic.
Finding positives amid the pandemic
With so much uncertainty, stress, and loss, it’s tough to talk about silver linings. But our peer group clients did mention a few positive developments they’ve observed, including an increase in awareness and appreciation of the EHS function at their companies. Developing their back-to-work responses has also allowed EHS practitioners to communicate and collaborate with different parts of the organization they hadn’t previously connected with often.
Preparing for the future
All the manufacturers in our peer group discussion are still dealing with significant issues related to employees returning to work. They are now considering how to overcome challenges with risk assessments and administrative controls to keep people safe in the “new normal.” However, with so many immediate issues to deal with, it is tough to think about how to plan and be ready for future disruptions.
Our guidance: It’s important not to lose focus, even during these immensely difficult times. Instead of creating all new tools and programs, use your existing ones to address the virus as you would other risks in the work environment. For example, use existing Job Hazard Analyses (if that is your company’s recognized tool), and add the COVID-19 risk to the analysis to determine what mitigations you can put in place.
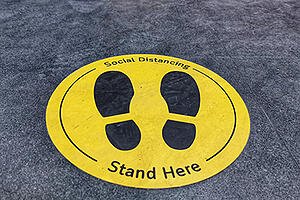
You can also set goals and leading and lagging indicators of performance to measure and adjust your organization’s approach to COVID-19. Examples of leading indicators you could consider for your organization include the number of COVID-19 facility audits performed per month, the number of contact tracing drills completed, and the closure rate and effectiveness of corrective actions. For lagging indicators, you might track the number of work-related COVID-19 events such as potential exposures or even the total number of quarantine hours logged by employees.
It was clear in this client peer group discussion that we are all looking for best practices and ideas and that no single organization has all the answers. The response to COVID-19 is the responsibility of us all to ensure the wellbeing of our employees, and it is a great time as EHS professionals to learn from each other.
For additional guidance we’ve provided to our clients and staff, read Resources to keep your manufacturing operations safe during COVID-19 and a guidance piece we produced on COVID-19 safety for both the home and workplace.
If you’re interested in participating in a future client peer discussion, please send me an email and be sure to let us know what topics you’d most like to discuss.
Published: 6/26/2020
Author
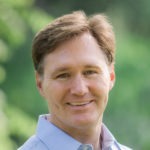
Senior Technical Expert