Burlington, Mass., October 29, 2024 — Environmental and engineering consultancy Haley & Aldrich announced today that its PFAS destruction technology, EradiFluor, destroyed nearly 100% of PFAS and measured and removed all PFAS below maximum contaminant levels (MCLs) in a recent field test at a U.S. Navy facility.
“These results, in addition to previously gathered lab data, show that EradiFluor is a powerful tool for the U.S. military, airports, industrial and manufacturing facilities, and others grappling with the problem of how to eliminate PFAS in water and liquid waste,” said John Xiong, Ph.D., P.E., the head of Haley & Aldrich’s Applied Research Program. Xiong led the team that developed EradiFluor over three years of testing and research.
The class of chemicals known as PFAS, or per- and polyfluoroalkyl substances, have often been referred to as “forever chemicals” because most available treatment technologies can only concentrate or transfer them to another form — not destroy them.
With this successful field test, EradiFluor becomes one of the few technologies on the market that can effectively destroy PFAS. It meets an urgent need for businesses and the public sector as state and federal regulatory scrutiny of PFAS grows. For example, the U.S. Environmental Protection Agency (EPA) adopted MCLs for six PFAS in drinking water in April 2024 that are in the parts per trillion (equivalent to one droplet of water in an Olympic-sized pool).
The field test shows EradiFluor’s potential as a practical solution to PFAS contamination challenges
The field test took place in mid-2024 at a Navy facility. Haley & Aldrich partnered with researchers from the University of California, Riverside — also partners in developing EradiFluor — to demonstrate the effectiveness of EradiFluor for treating liquid waste containing high levels of multiple PFAS that is produced from an in situ groundwater foam fractionation remediation system.
EradiFluor relies on ultraviolet light and common chemicals to destroy PFAS. It destroys PFAS molecules by breaking their carbon-fluorine bonds.
When treating the foam fractionate at the Navy facility, our team found consistent reductions of PFAS concentrations. All PFAS compounds were either non-detectable or met the strict EPA MCLs. Meanwhile, fluoride — the nontoxic product of the PFAS degradation process — increased in concentration, demonstrating complete defluorination (in other words, destruction) of PFAS.
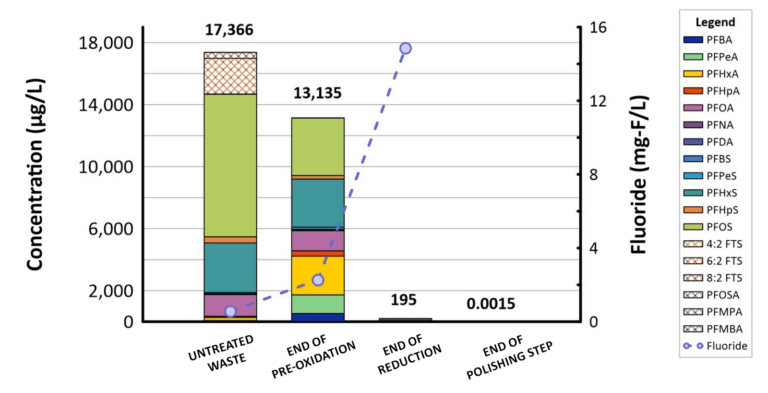
“EradiFluor is specifically designed to solve the persistent and expensive environmental problem of PFAS for many of our clients,” said Elie Haddad, P.E., a principal consultant in Haley & Aldrich’s Contaminated site management practice. “As more organizations need to address PFAS contamination, we hope to offer a solution that’s effective and practical.”
EradiFluor works at ambient temperature and pressure, so it requires less energy and is safer to operate than technologies that rely on high pressure and high heat. It’s also flexible and scalable: Users can deploy one or many of the small-footprint units on-site or ship waste to a central location for treatment.
The Department of Defense (DOD) backed EradiFluor’s development and testing with highly competitive funding from its Environmental Security Technology Certification Program and the Air Force Civil Engineering Center. Many DOD sites — such as the naval installation where we performed the field test — have used PFAS-containing foam to fight high-heat fires and train firefighters, so the DOD has an urgent need for innovative PFAS treatment technologies such as EradiFluor.
Other potential beneficiaries include industrial and manufacturing facilities that use and produce PFAS-containing waste via a host of processes, landfills that produce PFAS-rich leachate that requires treatment, and municipal water treatment plants that must treat water supplies to meet the EPA’s MCLs.
For more information:
Contact our Media team.